What is Porosity in Welding: Essential Tips for Getting Flawless Welds
Wiki Article
The Scientific Research Behind Porosity: A Comprehensive Guide for Welders and Fabricators
Understanding the elaborate systems behind porosity in welding is crucial for welders and makers making every effort for remarkable craftsmanship. From the structure of the base materials to the complexities of the welding procedure itself, a plethora of variables conspire to either aggravate or relieve the visibility of porosity.Comprehending Porosity in Welding
FIRST SENTENCE:
Evaluation of porosity in welding exposes vital understandings right into the integrity and high quality of the weld joint. Porosity, identified by the visibility of dental caries or gaps within the weld steel, is a typical worry in welding procedures. These spaces, otherwise appropriately attended to, can compromise the structural honesty and mechanical homes of the weld, bring about prospective failings in the ended up product.
To identify and measure porosity, non-destructive testing approaches such as ultrasonic testing or X-ray evaluation are commonly utilized. These methods permit the identification of interior flaws without jeopardizing the integrity of the weld. By examining the size, shape, and distribution of porosity within a weld, welders can make informed choices to enhance their welding procedures and attain sounder weld joints.

Variables Influencing Porosity Development
The occurrence of porosity in welding is influenced by a myriad of aspects, varying from gas protecting efficiency to the details of welding parameter settings. Welding specifications, consisting of voltage, present, take a trip rate, and electrode type, also impact porosity formation. The welding strategy utilized, such as gas steel arc welding (GMAW) or shielded metal arc welding (SMAW), can influence porosity formation due to variants in warm distribution and gas insurance coverage - What is Porosity.Impacts of Porosity on Weld Top Quality
The presence of porosity additionally weakens the weld's resistance to deterioration, as the entraped air or gases within the voids can respond with the surrounding setting, leading to degradation over time. In addition, porosity can hinder the weld's ability to endure pressure or effect, Full Article additional threatening the total high quality and dependability of the welded framework. In crucial applications such as aerospace, automotive, or structural buildings, where safety and longevity are extremely important, the detrimental impacts of porosity on weld top quality can have extreme consequences, highlighting the significance of minimizing porosity with appropriate welding strategies and treatments.Strategies to Lessen Porosity
In addition, using the appropriate welding parameters, such as the proper voltage, present, and travel rate, is critical in stopping porosity. Maintaining a consistent arc length and angle throughout welding likewise helps reduce the possibility of porosity.
Moreover, choosing the appropriate securing gas and maintaining proper gas flow prices are essential in decreasing porosity. Using the ideal Check This Out welding technique, such as back-stepping or employing a weaving activity, can also assist distribute warmth equally and lower the possibilities of porosity development. Making sure correct air flow in the welding atmosphere to remove any possible sources of contamination is essential for attaining porosity-free welds. By applying these methods, welders can effectively lessen porosity and generate high-quality bonded joints.
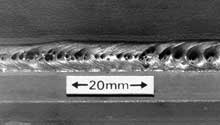
Advanced Solutions for Porosity Control
Implementing innovative technologies and cutting-edge approaches plays a pivotal function in accomplishing remarkable control over porosity in welding procedures. One advanced remedy is the usage of sophisticated gas mixes. Securing gases like helium or a mixture of argon and hydrogen can help in reducing porosity by offering far better arc stability learn the facts here now and boosted gas coverage. In addition, using sophisticated welding strategies such as pulsed MIG welding or modified atmosphere welding can additionally help alleviate porosity concerns.One more advanced option includes the use of sophisticated welding devices. For example, utilizing equipment with integrated features like waveform control and advanced source of power can enhance weld top quality and decrease porosity risks. The application of automated welding systems with specific control over parameters can considerably minimize porosity defects.
In addition, incorporating innovative surveillance and assessment innovations such as real-time X-ray imaging or automated ultrasonic testing can aid in discovering porosity early in the welding process, permitting instant restorative actions. In general, integrating these sophisticated solutions can significantly enhance porosity control and improve the total high quality of bonded elements.
Conclusion
In verdict, understanding the scientific research behind porosity in welding is vital for welders and makers to generate premium welds - What is Porosity. Advanced options for porosity control can even more boost the welding procedure and make sure a solid and reputable weld.Report this wiki page